

For nearly two decades, the University of California San Diego has been home to a key instrument for understanding earthquakes: a 40-by-25-foot steel platform that uses a hydraulic system to mimic seismic movements. This “shake table,” which can literally shake whatever is on top of it, is one of the largest in the world. It has been used to test more than 30 structures since it was opened in 2004, with the results informing changes to building codes and road regulations. But for the past nine months, the table has stood still as an unprecedented experiment was prepared for it: a bespoke 10-story wooden building, the highest ever to be put to a high-magnitude test.
According to principal investigator Shiling Pei, the goal of the aptly-named TallWood project is to prove that wooden buildings can withstand strong shaking without losing their structural integrity. With a lower carbon footprint than concrete or steel, wood has become an increasingly popular choice in recent years as a more sustainable building material. Plus, the flexibility of wooden structures makes them particularly well-suited to riding out earthquakes, Pei says—think about the ability of tree branches to bend without snapping. And while years of research and modeling allow him to endorse such buildings confidently, he is eager to demonstrate it in a real-world forum that will prove the power of wooden designs to a broader audience.
“It is proof that, using current technology, we can build a 10-story building and produce resilient results after earthquakes,” Pei said. “It is our plan to throw about 40 earthquakes at the building, and the building will not be damaged structurally.” At least, that’s the hope.
[Related: Why most countries don’t have enough earthquake-resilient buildings]
Pei, who is also a civil and environmental engineering professor at the Colorado School of Mines, specializes in timber systems and hazard mitigation through engineering, which makes him a unique fit for this project. But he’s just one part of the extensive, multidisciplinary team that has been working on this project since 2016 as part of the National Science Foundation’s Natural Hazards Engineering Research Infrastructure (NHERI) program. The team includes professionals from six universities, more than two dozen industry partners, and the United States Forest Service, among other government agencies.
Members of this team first put their timber theories to the test in 2017, building a two-story wooden building for the shake table. It held up successfully over the course of around 30 “earthquakes,” Pei said, including movements modeled after the 6.7-magnitude Northridge Earthquake, which happened nearly three decades ago in California.
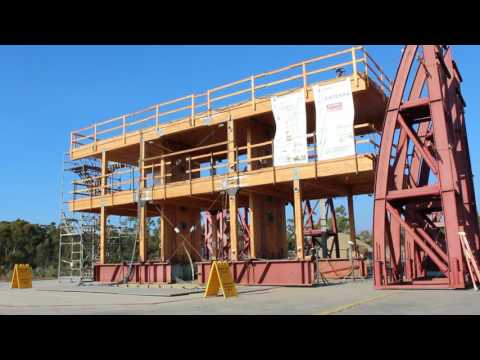
The 10-story TallWood project builds on that research, literally, not only in height but in design. At its core, it is a mass timber system, meaning it is comprised of layers of wood laminated together into solid panels, which can be put together in the desired form—like an “IKEA assembly on steroids,” as Pei describes it. While this model is being built for the shake table only, the hope is that the design could be replicated in the real world if successful.
The key to the earthquake-adaptive design are the so-called “rocking walls,” which are made to allow movement. Rather than the walls being firmly affixed to the foundation of steel base beams, which form the ground support for the shake table, they are placed on top, and held in position with steel bars that run up the entire structure. These bars act like rubber bands, keeping the walls in place but also affording some flexibility. So, if an earthquake were to occur, the rocking walls would shake and even lift up from the foundation, with the bars preventing them from moving too much out of line. This design attempts to prevent buildings from attaining the sort of structural damage that has been observed after past earthquakes, which can lead to collapse or be difficult to fix.
Other features like columns and bendable plates also help dissipate energy, while steel armoring helps mitigate any structural damage. Co-principal investigator Jeffrey Berman, a civil engineering professor at the University of Washington, described the overall composition during a NHERI radio interview as an essentially “damage-free structural system” since this design can accommodate an abundance of movement.
The TallWood building is also outfitted with nonstructural features like doors, windows, stairs, ceilings, and additional walls. Keri Ryan, an earthquake engineer at the University of Nevada Reno and another co-principal investigator with the project, explained in another NHERI radio interview that this is important for getting a fuller picture of how real wooden buildings would respond to earthquake stress.
“The earthquake engineering community has focused mainly on structural design in the past, but in past earthquakes, a lot of the damage is focused on nonstructural systems,” Ryan said, citing the Northridge Earthquake as one example of this phenomenon.
The ultimate hope is that the project reveals that a large wooden structure can be resilient to earthquakes, perhaps even performing better than a concrete, brick, or steel one, while at the same time being better for the environment overall.
While construction on the TallWood building was completed earlier this year, the team is still putting on final touches, including more than 700 sensors to record data like building displacement and acceleration. They are also installing dozens of cameras to actually see what the test looks like from various angles of the building since it will of course be empty during the simulated seismic shocks. The final step before the TallWood testing begins is to run smaller tests on the shake table to ensure the hydraulic-powered system is working properly after months at rest.
Once the plate is given the go-ahead for the official shaking to begin later this spring, those hundreds of data points will be compared to the research team’s models to see how they stacked up and if any adjustments need to be made. If all goes as expected and the building’s structural components remain intact, Pei said the TallWood team hope its design could be replicated in other buildings and used to inform future building codes. All of the data will eventually be shared in a publicly-accessible database, as well, allowing other researchers to integrate the data into their own models and experiments.
To stay updated on the next steps for TallWood, including testing dates, you can check out the project website. There are also livestream cameras aimed at the structure daily, which you can watch here.
Update on May 17: Watch video of the structure being tested, below.