

Since 3D printers debuted in the 1980s, the devices have been used to build meat, chocolate, human organs, clothing, cars, and houses. It’s more mainstream than ever, and you can buy a machine for less than $200.
Also called additive manufacturing or rapid prototyping, 3D printing has many advantages over the more traditional subtractive manufacturing methods, where you start with a hunk of metal or wood and remove material using mills, drills, and other tools. The two main benefits are that 3D printers produce a lot less waste and can do a better job creating objects with complex shapes. Instead of an involved assembly process, everything can be made in one place.
“Mass manufacturing methods, almost all of them are quite fixed,” says Diana Haidar, associate professor of mechanical engineering at Carnegie Mellon University. “You can only remake the exact same parts over and over again. But people also want custom parts. That’s where 3D printing has a niche.”
So how, exactly, does a 3D printer work?
What is 3D printing?
Consider the type of printing most people are very familiar with: Printing with ink on paper. This is 2D printing, because there’s an area with an x-axis and a y-axis, so there are two degrees of freedom. With 3D printing, there’s a third dimension: height. The files you feed into 3D printers are 3D images that a software program then slices into horizontal layers.
“The idea is that I have a 3D object, and I’m going to slice it into many individual layers. We use slicer software for that,” Haidar explains. “Then there’s usually a two-axis head that will move around and build a singular layer. Then either the head goes up or the bed [that the object is being built on] will drop. But there is a z-axis change so we can build up one layer at a time.”
Popular methods for 3D printing
One of the most common types of 3D printing is fused deposition modeling, or FDM. “It’s the cleanest with regards to space,” says Haidar.
With this method, there’s a spool of winding filament (usually plastic or polymer) that is fed into the machine’s head. Inside the head, there’s a heating unit that melts the polymer. Polylactic acid (a type of plastic) is one of the most commonly printed 3D materials, because it’s cheap and has a fairly low melting point of around 180 degrees Celsius (350 degrees Fahrenheit). When it’s used as a feeding material, engineers usually set the 3D printer to around 200 Celsius (390 Fahrenheit) to make sure the material is going to be melted as it’s extruded from a little nozzle, but can then harden back into form. The smaller the nozzle, the more resolution there is in the printed object.
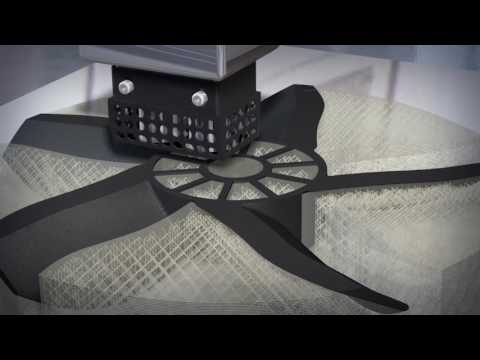
The second most popular method for 3D printing is an older technique called stereolithography, or SLA. In this case, photo-curable resin is the print material instead of a solid spool. This technique involves a bath of sticky, goopy resin sitting in a glass tank that’s uncured; a UV laser beam and multiple mirrors cure one layer at a time. Every time a layer is cured, it becomes solid, gets sheared from the bottom glass in the tank, and then gets lifted from the bath—eventually a solid, cohesive structure emerges.
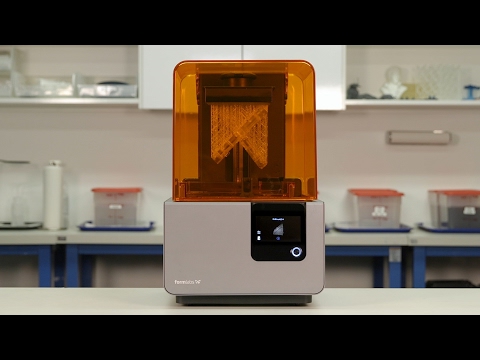
The third most popular 3D printing method is called laser powder bed fusion. This technique works well for printing or compressing together metals. To start, there is a big, flat bed of metal powder, and a laser carves out a shape, melting together the desired forms. Once a layer is complete, the bed drops, and a roller distributes a new fine layer of powder across the surface.

Another common 3D printing method is polyjet printing, which allows engineers to work with a wide array of nozzles and materials (from hard to soft) in one print.

What kinds of materials can be 3D printed?
Although 3D printers most commonly print with plastics, they can also be tweaked to print metal-embedded materials, ceramic-embedded materials, and wood-embedded materials. Different types of fibers or particles can be mixed in with polymer binders to give objects varied properties.
When specialized machines print organs (such as a heart), multiple nozzles can be prefilled with syringes to inject different types of cells. Instead of a spool, the machine injects into a hydrogel.
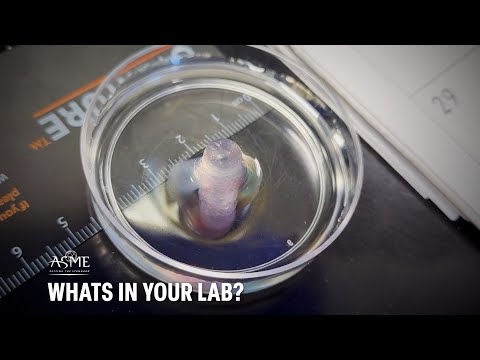
How much are 3D printers?
The cheapest 3D printer on the market is around $200, and those machines are the ones used by engineering students to make quick mockups. But spending less money on a machine like this comes with trade-offs. The cheap ones tend to be more finicky and break down more often. They’re also not as consistent at producing the same object over and over again. For example, the polymer, or plastic building material, can warp if there’s too drastic a change in temperature from the inside of the nozzle to the external environment. “You don’t see that as much in the big machines because they have clearly enclosed environments that are temperature-controlled, and they might even have a cooling cycle,” Haidar explains.
A midrange desktop machine for FDM printing will usually go for $3,000, and this price includes software packages. A more high-end machine that can manufacture bigger objects with a more durable starting material can cost $200,000. Spending all that money comes with big benefits down the line. “Your maintenance cost is quite a lot lower. It’s easier to print materials that the little machines would struggle with,” says Haidar. “Those machines give you the closest thing to a professionally manufactured part.”
The fanciest machines print using metal, like aluminum. The metal 3D printers can cost up to $1 million, since they have to be operated in a room that’s very well-controlled, ventilated, and has the ability to suppress explosions (if they happen).