

Researchers may have cracked the code on crafting practically zero-emission “reactivated cement” by recycling it with its partner-in-pollution, steel. The University of Cambridge team detailed their process in a study published on Wednesday in Nature—an “absolute miracle,” according to first author and professor of engineering and the environment, Julian Allwood.
One of the most sustainable measures society can adopt is reducing its reliance on concrete—and while alternatives now exist, transitioning to them is easier said than done. In the meantime, making cement’s production process greener would be very helpful. Everything from used diapers, to coffee grounds, to bacteria may be promising additives that cut back on the building material’s CO2 emissions, which comprise around 8 percent of the annual global total. But none of these fix the underlying issue—cement’s active ingredient, clinker. Industry experts and researchers have spent the past two decades looking into ways to use less of it, and while they can minimize the amount needed by mixing it with other products, there is currently no cement without at least some amount of clinker.
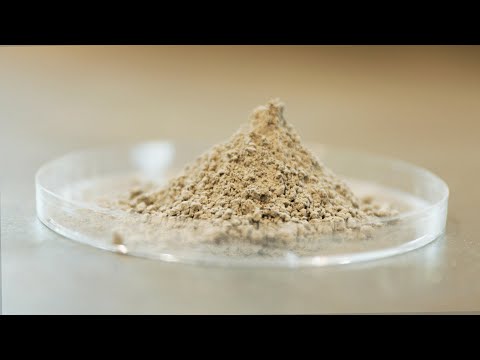
“Cement is a really difficult problem in mitigating the world’s greenhouse emissions, because we have no direct technical substitute for it,” Allwood explained in an accompanying university video.
As New Atlas highlighted Thursday, Allwood’s collaborator and study first author, Cyrille Dunant, had an inkling of a solution while conducting previous work in concrete recycling methods.
“I had a vague idea from previous work that if it were possible to crush old concrete, taking out the sand and stones, heating the cement would remove the water, and then it would form clinker again,” he said. “A bath of liquid metal would help this chemical reaction along, and an electric arc furnace, used to recycle steel, felt like a strong possibility. We had to try.”
The first step was to crush a demolished building’s waste concrete even more than usual to separate old cement from the leftover stone and sand. This “concrete paste” was then transferred to an electric arc furnace employed for steel recycling. Reforging steel requires something called a flux to bubble through its molten state and purify the metal, before creating an outer layer that protects steel from air. As it just so happens, concrete paste is an extremely effective flux substitute—although there’s a catch. Steel recycling ultimately produces a molten flux waste commonly known as slag. If you harvest the slag and cool it quickly enough, however, it will turn into the most commonly used variety of cement, called Portland cement, with a nearly identical chemical composition and durability. And if sustainable energy is used to power the electric arc furnaces, then the entire concrete-steel recycling method generates practically zero emissions.
[Related: Bacterial ‘blood’ could heal cracks in concrete.]
In its initial small trials, the new technique produced a few dozen kilograms of so-called “electric cement.” Allwood and Dunant’s team is now testing the process within its first industrial-scale experiments, where they hope to produce as much as 66 tons of reactivated cement within two hours. While they still need to conduct further scalability research, the collaborators are confident their method is up to the task—they are in the process of filing a patent on their procedure, and are working to partner with companies and government agencies to speed along development. If the new concrete can withstand the pressure, engineers estimate the possibly revolutionary solution could supply as much as a third of the UK’s cement needs by 2030—let alone what it could do for global industry sustainability.
As promising a procedure this may be, Allwood still cautioned that recyclable cement is only one part of a much larger issue.
“Producing zero emissions cement is an absolute miracle, but we’ve also got to reduce the amount of cement and concrete we use,” he said. “… [W]e just use far too much of it. We could [also] dramatically reduce the amount of concrete we use without any reduction in safety, but there needs to be political will to make that happen.”