Your disposable COVID masks could be reborn as fuel
Billions of single-use face masks and shields are discarded every day due to the pandemic.
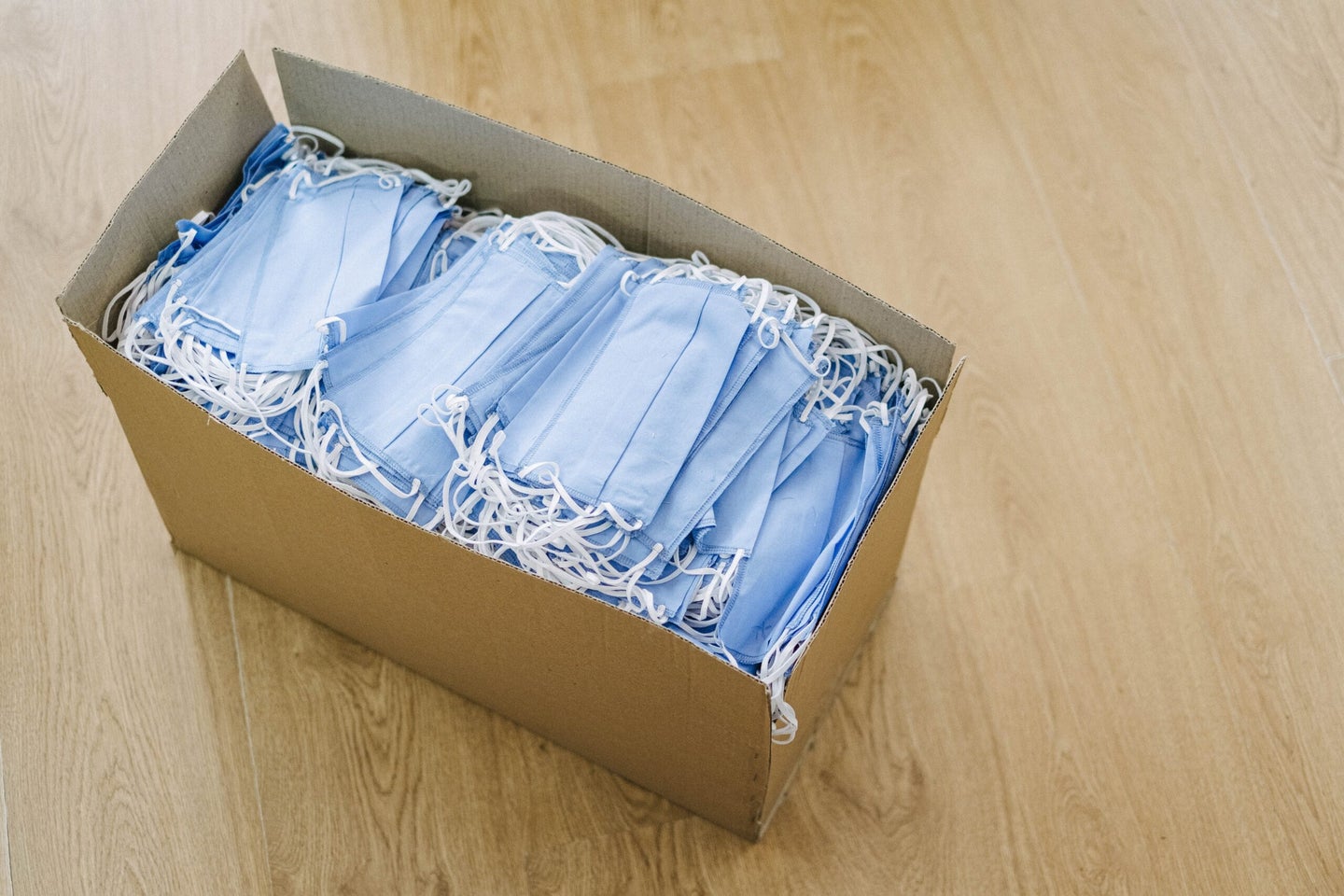
The demand for single-use plastic significantly increased when the COVID-19 pandemic began, especially with the steady need for personal protective equipment (PPE) such as surgical face masks, gloves, face shields, and gowns to prevent virus transmission. An estimated 3.4 billion single-use face masks or face shields are discarded every day due to the pandemic. Food packaging and plastic bag waste in households also multiplied with the increase in online shopping and delivery services.
Improper waste management will only aggravate existing global pollution and endanger the lives of both people and animals. It’s necessary to come up with an effective strategy that will minimize the environmental impact of the continuous COVID-19 waste stream—and some scientists think turning trash into fuel could be an option.
Numerous studies propose that COVID-19 waste could be converted to fuel
Several studies over the past two years have proposed pyrolysis—an effective method that will not only mitigate plastic pollution but also convert waste into usable fuel. A 2020 study published in Biofuels proposed that discarded PPE kits be converted into liquid fuel through the process, which is the thermal decomposition of a solid material. Pyrolysis heats the material to a temperature high enough to deconstruct polymers.
“Typically, when we talk about pyrolysis as a technology, we heat a solid up without oxygen and then collect the vapors as an oil,” says George Huber, director of the Center for Chemical Upcycling of Waste Plastics who was not involved in the study. “Pyrolysis of plastics is a technology that is being used to produce oils from plastics. These oils can then be used to make new plastics or fuels.”
[Related: Humans created an extra 8 million tons of plastic waste during the pandemic.]
According to a 2021 study published in Chemosphere, pyrolysis is an environmentally friendly, efficient, and cost-effective COVID-19 waste management technique. “Considering the advantageous nature of pyrolysis techniques and its capacity in effective dealing of municipal wastes, the same can be enforced for the treatment of COVID-19 waste. The technology utilizes high-temperature combustion, which can be applied for complete degradation of the infectious agents that are carried along with the COVID-19 waste,” the researchers said.
Face masks and surgical gloves can be easily converted into fuel because they are made of polypropylene and polyvinyl chloride, which are thermoplastic polymers with high oil content. The oil obtained through pyrolysis is comparable with commercial fuel because its properties are similar to that of fossil fuels.
A 2022 study published in Bioresource Technology converted surgical masks into liquid oil and found that its higher heating value is 43.5 megajoules per kilogram, which is only slightly lower than that of diesel fuel and gasoline at 45.8 and 46.3 MJ/kg respectively.
Although pyrolysis is a promising method of processing waste PPE, assessing its overall energy and environmental sustainability is still a crucial step.
Pyrolysis-based waste processing systems would produce fewer carbon dioxide emissions
In a life-cycle assessment (LCA) conducted by the authors of the Bioresource Technology study, the researchers found that processing waste through pyrolysis produces fewer carbon dioxide and phosphorus emissions than most conventional waste management approaches.
A different 2022 study published in Renewable and Sustainable Energy Reviews also proposed an optimal pyrolysis-based PPE waste processing system that could reduce the use of fossil fuels by 31.5 percent and produce 35.04 percent fewer greenhouse gas emissions compared to the incineration process. Compared to their proposed system, the landfilling process poses 143 and 46 percent higher environmental impacts on marine ecotoxicity and human toxicity.
[Related: This new recycling system could keep COVID PPE out of landfills.]
Effective waste treatment mitigates plastic pollution, eliminates the risk of viral infection, and compensates the heavy fossil fuel use in PPE production, says Fengqi You, study author and professor at Cornell University. With their framework, PPE waste could be collected and transported into pre-processing and decontamination facilities. Afterward, it will then be brought to integrated pyrolysis plants for conversion into downstream, value-added products such as gasoline, diesel, and propane, among others. Not to mention, the system can handle waste mixtures as opposed to only a specific type of PPE, says You.
That’s the benefit of pyrolysis as a technology—it can convert all plastic feedstocks into an oil, says Huber. Despite all the research, there have yet to be any implementations of the proposed methods on a large scale. Last September, the U.S. Environmental Protection Agency (EPA) solicited real-world cost, design, process, and environmental information about pyrolysis technologies to assist in the potential development of regulations for it, given that the country is still in the early stages of development of the technology.
However, according to a 2020 report, by the Global Alliance for Incinerator Alternatives (GAIA), converting plastics into fuel would not contribute to a circular economy because it does not produce new plastics. It would be difficult for pyrolysis to produce oil that can be used to make new plastic, and doing so would require additional chemical processing and massive amounts of energy, according to the report.
Still, some researchers are ready to make our old masks into new fuels. “The technologies [to treat PPE waste effectively] already exist and were proved to be economically and environmentally efficient while protecting public health and mitigating climate changes,” says You. “The next step is scaling up the technology and process.”