Synthetic, Self-Healing Skin That’s Sensitive To The Touch
Human skin is a hard system to emulate, but that hasn't stopped Stanford scientists from producing a touch-sensitive material that can heal itself at room temperature.
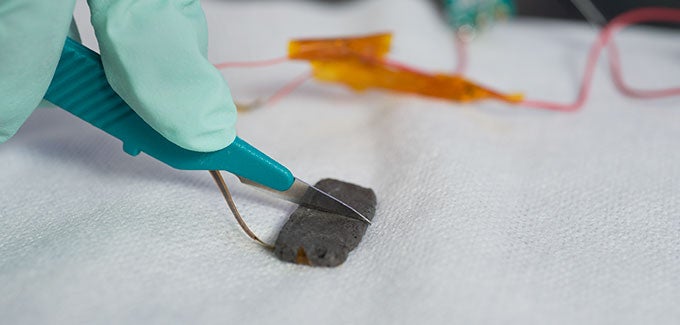
Before we can construct the realistic humanoid robots that populate our most vivid sci-fi-driven dreams, there are a lot of human systems that researchers are going to have to emulate synthetically. Not the least challenging is human skin; filled with nerve endings and able to heal itself over time, our skin serves as both a massive sensory system and a barrier between our innards and the outside world. Now, an interdisciplinary team of Stanford researchers has created the first synthetic material that is both self-healing at room temperature and sensitive to touch–a breakthrough that could be the beginnings of a new kind of robot skin (and in the meantime enjoy much more practical applications like enhanced prosthetics).
The Stanford material is far from the first self-healing plastic or polymer, but it does enjoy some benefits that set it apart. For one, many self-healing materials require some kind of catalyst or special condition to heal up, things like exposure to high temperature or certain spectrums of light. Others can heal up at room temperature, but they generally can only do so once–the act of healing alters their chemical structure such that they cannot do it a second time, much less a third or fourth.
Then, if an analog for skin is what you’re truly looking for, there’s the problem with touch sensitivity. Most plastics, polymers, and such–the primary materials used in self-healing research–are fantastic insulators. But to imbue a material with a sense of touch–and to make it interface with a larger digital system–you really want something conductive. That’s where the Stanford team has really broken new ground. Its material can repair cuts or tears in itself at room temperature multiple times, and it is conductive.
How did the researchers pull it off? They started with a plastic consisting of molecular chains joined by simple hydrogen bonds. This imparts the self-healing ability, as the bonds can be easily broken but also easily reconstituted by simply putting the broken chains back in contact with each other. In the lab, the researchers severed a piece of the material completely, creating two separate halves. After pressing the cut edge back together for just a few seconds, three-quarters of its prior strength had been restored. Within half an hour it returned to nearly 100 percent strength. After 50 such trials, the material still healed up nicely.
Then, to achieve conductivity, the researchers distributed nickel particles throughout their plastic. These nickel particles not only increase the material’s mechanical strength, but also serve as a means for electrons to move through the material, hopping from one particle to the next, creating an electric current. Bending, flexing, or otherwise warping the material changes the distance between the nickel particles, altering the material’s resistance to the current. That electrical resistance can be measured to determine the shape of the skin and any pressure being exerted on it.
It’s easy to envision something like this being integrated into future prosthetics to help restore a sense of touch to those missing a limb. More immediately, such a material could be used to sheathe other electronics to give them a self-healing capacity. The findings were published in the November 11 issue of the journal Nature Nanotechnology.